Living Processes
Lived processes and workflows are well connected
with each other and with the management system,
thereby representing a living company
and are continuously improved
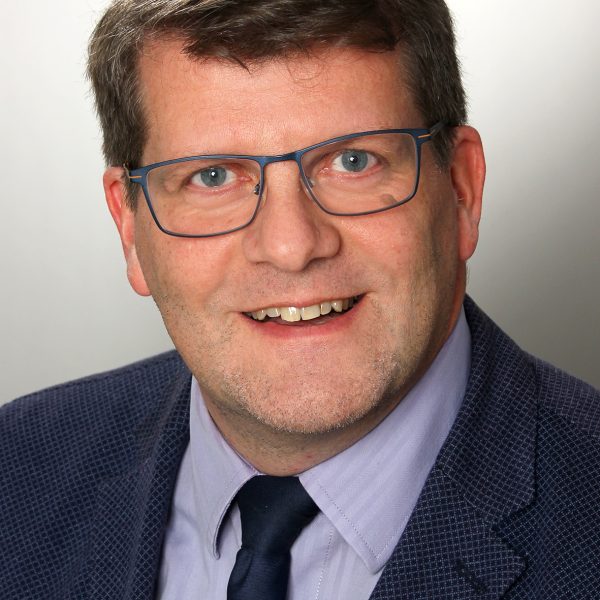
Welcome
I am Martin Holling, Industrial Engineer (Diplom-Wirtschaftsingenieur) and Process Management Nerd since more than 25 years
In management consulting, I focused on supporting medium-sized to large companies in the fields of energy production, mechanical engineering, medical technology, petrochemicals and trade in the areas of process management, digitalization and IT project management.
I was responsible for the business process management of part of a large multinational corporation and took responsibility of the harmonization and optimization of the business processes of 85,000 employees worldwide.
I was a member of the core BPM team for this corporation and helped to develop the principles of Business Process Management in the corporation.
But I also know that it can be done on a small scale, I wrote my diploma thesis for a medium-sized company with the topic of process management.
I want to promote the implementation of BPM in medium and small companies with the help of the LEAN management approach.
There is certainly a lot of possibilities…!
expertise
My experiences
Business Process Management
Business Process Management enables goal-oriented control of operational, management and support processes and aligns them with the needs of customers, employees and suppliers.
Quality Management
Standardization, harmonization and continuous improvement of processes are core elements of quality management and business excellence.
Integrated Management System
The Integrated Management System for Quality, Environmental Protection, Occupational Health and Safety (QEHS) standardizes the structures and processes of quality management, environmental management and occupational health and safety. Synergies are exploited through harmonized processes.
Process Maturity Assessment
In order to systematically ensure and continuously develop quality in the processes, a company-wide standard is required for the management of all operational, management and support processes.
Digitization
Optimize processes effectively to the respective needs of the users and integrate them cleanly in daily work. The bottom line is that this results in lean and effective workflows that position the company optimally on the market
Lean SixSigma
It is absolutely essential for small and medium-sized companies to document and implement the processes they work in as simply as possible (LEAN). This is the best basis for continuous improvement of the processes and thus of the entire system.
Human Centric BPM
The company-wide framework requirements should be deliberately kept simple, lean and pragmatic, and focus on the benefits for the process user. The main principles and goals of an effective process management approach are simplification, user-friendliness and clarity.
Process oriented Organization
We know WHAT we want to do, so we first clarify HOW we will do it. Once we have defined the workflow, we immediately see very clearly WHO we need to do it with to make it happen as effectively as possible!
Topics!
My view on:
Process Management
Companies can only be successful if all employees really pull together. This is especially true for small and medium-sized companies. Here, failure costs due to process weaknesses are very quickly the beginning of the end, because the company cannot spare any substance to cover these costs.
Today, process management is mainly done on a large scale with extreme use of personnel and IT tools. This is overkill for small and medium-sized companies. Nevertheless, process management is also necessary here.
For small and medium sized companies it is therefore absolutely necessary to document and implement the lived processes as simple as possible (LEAN). This is the best basis for a continuous improvement of the workflows and thus of the entire system.
Living Processes: the lived processes and workflows should be well connected with each other and with the management system in order to represent and further develop a correspondingly living company.
In everyday life, habit creeps into the processes and prevents an optimal design and development of the processes. The independent view from the outside with a clear focus on the internal know-how results in the possibility to design and document the lived processes effectively and efficiently at any time, which also provides, quasi as a waste product, the ideal prerequisite for a certification of management systems (QMS EHS-MS, ...). Active process management also reduces the effort required for regular monitoring audits and re-certifications.
Lean Process Optimization
In order to systematically ensure and continuously develop quality in the processes, a company-wide standard for the management of all operational, management and support processes is required.
These company-wide framework requirements should be deliberately kept simple, lean and pragmatic and focus on the benefits for the process user.
The main principles and goals of an effective process management approach are simplification, user-friendliness and clarity.
Business Process Management enables goal-oriented control of operational, management and support processes and aligns them with the needs of customers, employees and suppliers.
World-class products and efficient and effective processes create tangible benefits for customers, employees, business partners and society and lead to sustainable corporate success:
- Short development cycles (time to market)
- Effective communication
- Efficient employee deployment
- Culture of continuous improvement
Standardization of processes is a key success factor. LEAN management elements, such as those defined and applied in the Toyota Production System (TPS), help to optimize processes effectively to the respective needs of the users and to integrate them cleanly in daily work. This results in lean and effective workflows, which position the company optimally in the market and help to identify and eliminate unnecessary resources (time, manpower, material,...).
Standards create the basis for:
- Efficiency in training and further development of employees
- smooth cooperation of all process participants
- Exchange of experience of successful procedures
- Leveraging of synergies by creating more transparency
- Rapid adaptation to changes in economic conditions
- Use of standard IT solutions
Process Oriented Organization
These organizations are usually structure-oriented, geographically or historically characterized. These organically developed organizations are usually not suitable for optimal workflows!
A company often starts with a product idea - WHAT do we want to do?
The necessary experts are then gathered to implement this idea - WITH WHOM do we do it?
In the beginning, the number of employees is manageable and everyone knows exactly what needs to be done. As the company grows, at some point you realize that not everyone knows on their own what their role in the company is. It has to be clarified HOW we have to do a job. Process management is born. But we are now trying to align work processes with the established organization - what a waste!
If it is possible to make a clean cut, the swing to a process-oriented organization is the obvious choice: We know WHAT we want to do, so we first clarify HOW we will do it. Once we have defined the workflow, we immediately see very clearly WHO we need to do it with to make it happen as effectively as possible!
In this way we create an optimized enterprise, which fulfills its enterprise purpose LEAN, thus under as optimal as possible avoidance of waste thus effectively and particularly competitively. With the same number of employees we create substantially more output or need substantially fewer resources for the same output. In any case, a cost-optimized solution.
integrated Management System
An Integrated Management System is not limited to ISO standards 9001 (quality management), 14001 (environmental protection management) and OHSAS 18001 (occupational health and safety), but can include all standards and management systems that are important for a company (for example, also business continuity management).
In cooperation with the company, the optimized Integrated Management System is created, implementation is supported and, if required, certification by an accredited certification company is prepared. The basis for this is the optimized lean processes and LEAN process management, which can provide all the documentation and evidence required for certification along the way.
Living Processes - lived Processes
For small and medium sized companies it is therefore absolutely necessary to document and implement the lived processes as simple as possible (LEAN). This is the best basis for a continuous improvement of the workflows and thus of the entire system.
Living Processes: the lived processes and workflows should be well connected with each other and with the management system in order to represent and further develop a correspondingly living company.
In everyday life, habit creeps into the processes and prevents an optimal design and development of the processes. The independent view from the outside with a clear focus on the internal know-how results in the possibility to design and document the lived processes effectively and efficiently at any time, which also provides, quasi as a waste product, the ideal prerequisite for a certification of management systems (QMS EHS-MS, ...). Active process management also reduces the effort for regularly due surveillance audits and re-certifications."
The moment a business owner can no longer gather all employees in one room to clarify, explain and commit employees to apply a course of action, a process management approach must be started at the latest.
Companies can only be successful if all employees really pull together. This is especially true for small and medium-sized companies. Here, failure costs due to process weaknesses are very quickly the beginning of the end, because the company cannot spare any substance to cover these costs. Today, process management is mainly done on a large scale with extreme use of human resources and IT tools. This is overkill for small and medium-sized companies. Nevertheless, process management is also necessary here.